List all the implementation steps for Oracle eAM module ?
1) Setting Up Organizations
2) Enabling Organizations for Enterprise Asset Management
3) Defining eAM Parameters
4) Setting Up Areas
5) Defining Departments and Resources
6) Defining Department Approvers
7) Defining Miscellaneous Documents
8) Defining Lookups including
- Activity Types
- Activity Causes
- Activity Sources
- Asset Activity Priorities
- Cost Category Codes
- Criticality Codes
- Asset Import Scope Codes
- Asset Import Statuses
- Contact Preferences
- Work Request Statuses
- Work Request Types
- Work Order and Work Request Priority Codes
- Work Order Reconciliation Codes
- Work Order Types
9) Setting Up Category Codes
10) Defining Asset Groups
11) Defining Activities
12) Activity Association Templates
13) Setting Up Attribute Groups
14) Defining Asset Documents
15) Defining Asset Numbers
16) Defining Asset Routes
17) Setting Up Asset Bills of Material
18) Defining Activities
19) Navigating the Activity Workbench
20) Defining Maintenance Routes
21) Setting Up Maintenance Bills of Material
22) Associating Asset Numbers with Activities
23) Creating Activity Templates
24) Defining Rebuildable Items
25) Defining Rebuildable Serial Numbers
26) Rebuildable Item/Activity Association
27) Defining Rebuildable Bills of Material
28) To set up a Non-Stock Direct Item
29) Project and Task Setup
30) Defining Meter Templates
31) Defining Meters
32) Associating Meter Templates with Asset Groups
33) Associating Meters with Asset Numbers
34) Defining Set Names
35) Defining a Preventive Maintenance Template
--
Posted By OracleOnDemand to Oracle Applications at 12/30/2008 10:21:00 PM
Tuesday, December 30, 2008
[Oracle Applications] Which responsibilities are automatically created during...
Which responsibilities are automatically created during installation process of EAM ?
When installing Oracle Enterprise Asset Management, the installation process automatically creates the following five responsibilities:
a) Oracle Enterprise Asset Management
b) Maintenance User Workbench
c) Maintenance Super User
d) Self-Service Work Requests
e) Self Service Time and Expenses
The 'Oracle Enterprise Asset Management' responsibility mentioned above is a super user responsibility. It includes the necessary functions to set up and implement Oracle Enterprise Asset Management.
--
Posted By OracleOnDemand to Oracle Applications at 12/30/2008 09:04:00 PM
When installing Oracle Enterprise Asset Management, the installation process automatically creates the following five responsibilities:
a) Oracle Enterprise Asset Management
b) Maintenance User Workbench
c) Maintenance Super User
d) Self-Service Work Requests
e) Self Service Time and Expenses
The 'Oracle Enterprise Asset Management' responsibility mentioned above is a super user responsibility. It includes the necessary functions to set up and implement Oracle Enterprise Asset Management.
--
Posted By OracleOnDemand to Oracle Applications at 12/30/2008 09:04:00 PM
[Oracle Applications] Which are pre-requisites for installing EAM module ?
Which are pre-requisites for installing EAM module ?
a) Configuring Concurrent Managers and Printers
b) Set up Responsibilities and assigning responsibilities as per requirements
c) Setting up Workflow module if work request(s) require approval from a maintenance department user
--
Posted By OracleOnDemand to Oracle Applications at 12/30/2008 09:00:00 PM
a) Configuring Concurrent Managers and Printers
b) Set up Responsibilities and assigning responsibilities as per requirements
c) Setting up Workflow module if work request(s) require approval from a maintenance department user
--
Posted By OracleOnDemand to Oracle Applications at 12/30/2008 09:00:00 PM
[Oracle Applications] Mandatory and Optional Oracle Applications modules for ...
To work with EAM, which are the Mandatory and Optional Oracle Applications modules/products?
Mandatory modules are
a) Inventory
b) Bills of Material
c) Cost Management
d) Work in Process
e) Manufacturing Scheduling
f) Quality
g) Human Resource
Optional modules are
a) MS/MRP
b) Fixed Assets
c) Oracle Financials modules
d) iProcurement
e) Purchasing
f) Order management
g) Oracle Projects
h) Property Manager
i) Project Manufacturing
j) Time and labor
k) Oracle Service
--
Posted By OracleOnDemand to Oracle Applications at 12/30/2008 08:54:00 PM
Mandatory modules are
a) Inventory
b) Bills of Material
c) Cost Management
d) Work in Process
e) Manufacturing Scheduling
f) Quality
g) Human Resource
Optional modules are
a) MS/MRP
b) Fixed Assets
c) Oracle Financials modules
d) iProcurement
e) Purchasing
f) Order management
g) Oracle Projects
h) Property Manager
i) Project Manufacturing
j) Time and labor
k) Oracle Service
--
Posted By OracleOnDemand to Oracle Applications at 12/30/2008 08:54:00 PM
Monday, December 29, 2008
[Oracle Applications] What is a kit ? How does it differ from PTO ?
What is a kit ? How does it differ from PTO ?
A kit is a PTO item which consists of a standard list of mandatory components (or included items) i.e standard bills of material which you pick, pack and ship when you process a customer sales order for that item. A kit is similar to a pick–to–order model because it has shippable components, but it has no available options to choose like PTO model and customer places a sales order directly by its item code number and not by using the configuration window (selecting from various options).
In Oracle Inventory module, kit item type and kit item template are pre-defined by Oracle and are supplied along with software.
An example of a product kit is a motor car maintenance kit which consists spanners, jack etc.It is quite possible that each kit component is in different stock keeping unit( SKU). The word 'Kitting' is used when you make a kit after picking it's components from subinventory/ies and pack it. For example making a bundle of a kit components is called kitting. In short, kit is a bundle of various mandatory components which a merchant /manufacturer sells as a master product.
--
Posted By OracleOnDemand to Oracle Applications at 12/29/2008 09:49:00 PM
A kit is a PTO item which consists of a standard list of mandatory components (or included items) i.e standard bills of material which you pick, pack and ship when you process a customer sales order for that item. A kit is similar to a pick–to–order model because it has shippable components, but it has no available options to choose like PTO model and customer places a sales order directly by its item code number and not by using the configuration window (selecting from various options).
In Oracle Inventory module, kit item type and kit item template are pre-defined by Oracle and are supplied along with software.
An example of a product kit is a motor car maintenance kit which consists spanners, jack etc.It is quite possible that each kit component is in different stock keeping unit( SKU). The word 'Kitting' is used when you make a kit after picking it's components from subinventory/ies and pack it. For example making a bundle of a kit components is called kitting. In short, kit is a bundle of various mandatory components which a merchant /manufacturer sells as a master product.
--
Posted By OracleOnDemand to Oracle Applications at 12/29/2008 09:49:00 PM
[Oracle Applications] What is Configure to order (CTO) ?
What is Configure to order (CTO) ?
It is a method of manufacturing which allows you, or your customer, to choose a base product at the very moment of ordering and then configure all the variable parameters (features) associated with that product from defined/available options.
Based on these selections, configurable items on each quote or order typically generates the unique product configuration and manufacturing routing and/or bill of materials based on various features and options. Vendor/order receiving company subsequently builds that configuration dynamically upon receipt of the order. The ability of the vendor to make and deliver products customized to specific customer needs offers a powerful competitive edge over competitors.
CTO is an environment in which the product or service is assembled or kitted on receipt of the sales order. Oracle EBS supports the Configure to Order environment with a range of features in order entry, demand forecasting, master scheduling, production, shipping, and financial accounting.
Configure to Order includes Pick-to-Order (PTO) and Assemble-to-Order (ATO) items, models, and hybrids. It supports building configurations using other configurations as sub-assemblies (multi-level configure-to-order), internal and external sourcing of ATO models at any level in the BOM and supports multi-level PTO/ATO hybrids.
--
Posted By OracleOnDemand to Oracle Applications at 12/29/2008 09:42:00 PM
It is a method of manufacturing which allows you, or your customer, to choose a base product at the very moment of ordering and then configure all the variable parameters (features) associated with that product from defined/available options.
Based on these selections, configurable items on each quote or order typically generates the unique product configuration and manufacturing routing and/or bill of materials based on various features and options. Vendor/order receiving company subsequently builds that configuration dynamically upon receipt of the order. The ability of the vendor to make and deliver products customized to specific customer needs offers a powerful competitive edge over competitors.
CTO is an environment in which the product or service is assembled or kitted on receipt of the sales order. Oracle EBS supports the Configure to Order environment with a range of features in order entry, demand forecasting, master scheduling, production, shipping, and financial accounting.
Configure to Order includes Pick-to-Order (PTO) and Assemble-to-Order (ATO) items, models, and hybrids. It supports building configurations using other configurations as sub-assemblies (multi-level configure-to-order), internal and external sourcing of ATO models at any level in the BOM and supports multi-level PTO/ATO hybrids.
--
Posted By OracleOnDemand to Oracle Applications at 12/29/2008 09:42:00 PM
[Oracle Applications] What is Pick to Order (PTO) ?
What is Pick to Order (PTO) ?
It is a configure-to-order environment where the options and included items in a PTO model (finished good) appear on pick slips after you receive the sales order from customer. Pickers gather the options (based on selection rules), the predefined shippable products parts/components or service from their predefined locations using pick slip and then ship the order. It is assumed that options and components quantity are readily available. It is an alternative to manufacturing the parent item on a work order and then shipping it. There is no additional value added after getting the customer order.
For Example: Computer System (CPU, Monitor and Printer) A pick to order model can have PTO option class, PTO items, ATO model, ATO Option class and ATO option items. There can not be any PTO model, PTO option class or PTO item under an ATO model. You want to manufacture a promotional laptop computer, you need laptop computer, dikettes, accessories and battery pack. Here, you define PL computer as PTO model, laptop computer as ATO model, battery pack, diskette and accessories as purchase items.
Standard, model and option class Bills of material, can include bills for pick-to-order bills, Pick-to-order is also an item attribute that you can apply to standard, model, and option class items. Oracle Master Scheduling/MRP and Supply Chain Planning does not support planning for pick-to-order models and option classes. Pick to Order (PTO) items have the Pick Component attribute set to Yes. Pick-to-order bills cannot have fractional component quantities if Oracle Order Management is installed. You cannot create routings for planning or pick-to-order items.
--
Posted By OracleOnDemand to Oracle Applications at 12/29/2008 09:29:00 PM
It is a configure-to-order environment where the options and included items in a PTO model (finished good) appear on pick slips after you receive the sales order from customer. Pickers gather the options (based on selection rules), the predefined shippable products parts/components or service from their predefined locations using pick slip and then ship the order. It is assumed that options and components quantity are readily available. It is an alternative to manufacturing the parent item on a work order and then shipping it. There is no additional value added after getting the customer order.
For Example: Computer System (CPU, Monitor and Printer) A pick to order model can have PTO option class, PTO items, ATO model, ATO Option class and ATO option items. There can not be any PTO model, PTO option class or PTO item under an ATO model. You want to manufacture a promotional laptop computer, you need laptop computer, dikettes, accessories and battery pack. Here, you define PL computer as PTO model, laptop computer as ATO model, battery pack, diskette and accessories as purchase items.
Standard, model and option class Bills of material, can include bills for pick-to-order bills, Pick-to-order is also an item attribute that you can apply to standard, model, and option class items. Oracle Master Scheduling/MRP and Supply Chain Planning does not support planning for pick-to-order models and option classes. Pick to Order (PTO) items have the Pick Component attribute set to Yes. Pick-to-order bills cannot have fractional component quantities if Oracle Order Management is installed. You cannot create routings for planning or pick-to-order items.
--
Posted By OracleOnDemand to Oracle Applications at 12/29/2008 09:29:00 PM
[Oracle Applications] What is Assemble-to-Order (ATO) Manufacturing ?
What is Assemble-to-Order (ATO) Manufacturing ?
ATO simplifies the process of manufacturing finished goods. These goods are standard products and are often configured by customers from Bills of material, where you can define available options for unique product configurations. Based on forecasting, subassemblies are manufactured prior to receiving the customer order and when the order is received, the stocked subassemblies and components are assembled to make the finished products. It is an environment where you open a final assembly order to assemble items that customers orders. It is manufacturing method/strategy which allows a product to be made or service to be available to meet the needs of a specific customer order. While producing finished goods on a large scale, this requires sophisticated planning processes which master schedules ATO models and options and then create work orders to build the unique configuration in WIP module while maintaining control of inventory, planning, cost accounting and Bills of Material. Planning process also anticipates changing demand for external or internal components or accessories and at the same time focuses on product customizations for individual customers.
WIP, Order Management and Shipping modules support building and shipping of ATO configurations. A discrete job is created from a configuration. An assemble to order item/assembly then can be linked to a sales order. Assemble-to-order is also an item attribute in Inventory module that you can apply to standard, model, and option class items. In Bills of Material module, a model bill can be either assemble-to-order or pick-to-order and an option class bill can be either assemble-to-order or pick-to-order. Assemble–to–Order Model (ATO Configuration) is a Model bill of material with optional items and option selection rules or Configuration manufactured from mandatory components and selected options, or purchased from a supplier. An ATO model can have ATO option class, ATO Option item, PTO Option Class and PTO Option item under it. ATO Model can be a finished good or it be a part of another bills i.e it is component on another bill. Assemble-to-Order Item is a Standard bill of material with mandatory standard components or Item manufactured from mandatory standard components, or purchased from a supplier.
For Example: Automobiles, computer manufacturing.
Suppose you want to produce a laptop computer. Then, it requires carrying case, key board, CPU, Monitor and Operating system. While defining a bills of material for laptop computer, you can define computer as ATO Model. A Model comes at the top of the configuration hierarchy, second comes the Option Class and then the Option item. Carrying case and keyboard are purchased items under the bill of laptop. CPU, monitor and Operating system are option classes and 386 processor and 486 processor are optional items under the option class CPU. Similarly ,you can have optional item under other option classes. It is quite possible that ATO Model itself is component on another bills of material.
--
Posted By OracleOnDemand to Oracle Applications at 12/29/2008 09:06:00 PM
ATO simplifies the process of manufacturing finished goods. These goods are standard products and are often configured by customers from Bills of material, where you can define available options for unique product configurations. Based on forecasting, subassemblies are manufactured prior to receiving the customer order and when the order is received, the stocked subassemblies and components are assembled to make the finished products. It is an environment where you open a final assembly order to assemble items that customers orders. It is manufacturing method/strategy which allows a product to be made or service to be available to meet the needs of a specific customer order. While producing finished goods on a large scale, this requires sophisticated planning processes which master schedules ATO models and options and then create work orders to build the unique configuration in WIP module while maintaining control of inventory, planning, cost accounting and Bills of Material. Planning process also anticipates changing demand for external or internal components or accessories and at the same time focuses on product customizations for individual customers.
WIP, Order Management and Shipping modules support building and shipping of ATO configurations. A discrete job is created from a configuration. An assemble to order item/assembly then can be linked to a sales order. Assemble-to-order is also an item attribute in Inventory module that you can apply to standard, model, and option class items. In Bills of Material module, a model bill can be either assemble-to-order or pick-to-order and an option class bill can be either assemble-to-order or pick-to-order. Assemble–to–Order Model (ATO Configuration) is a Model bill of material with optional items and option selection rules or Configuration manufactured from mandatory components and selected options, or purchased from a supplier. An ATO model can have ATO option class, ATO Option item, PTO Option Class and PTO Option item under it. ATO Model can be a finished good or it be a part of another bills i.e it is component on another bill. Assemble-to-Order Item is a Standard bill of material with mandatory standard components or Item manufactured from mandatory standard components, or purchased from a supplier.
For Example: Automobiles, computer manufacturing.
Suppose you want to produce a laptop computer. Then, it requires carrying case, key board, CPU, Monitor and Operating system. While defining a bills of material for laptop computer, you can define computer as ATO Model. A Model comes at the top of the configuration hierarchy, second comes the Option Class and then the Option item. Carrying case and keyboard are purchased items under the bill of laptop. CPU, monitor and Operating system are option classes and 386 processor and 486 processor are optional items under the option class CPU. Similarly ,you can have optional item under other option classes. It is quite possible that ATO Model itself is component on another bills of material.
--
Posted By OracleOnDemand to Oracle Applications at 12/29/2008 09:06:00 PM
Sunday, December 28, 2008
[Oracle Applications] Oracle Enterprise Asset Management (eAM) module - An In...
What are aims, objects and benefits of Oracle Enterprise Asset Management (EAM) module ?
1) An asset is an entity for which users can report problems. Assets can be cooling towers, cranes, buses, buildings, conveyors, or anything that needs work.
2) eAM creates and implements maintenance procedures for both assets and rebuildable Inventory items and takes care of comprehensive and routine maintenance requirements of asset intensive organizations. It effectively maintains assets such as vehicles, cranes and HVAC systems and rotable Inventory items such as motors and engines.
3) eAM enables users to optimally plan and schedule maintenance operations /activities with minimal disruptions to an organization's operations and productions. It measures performance and optimizes maintenance operations. It tracks the performance of the assets and rebuildable inventory items by using meters, quality plans and conditioning systems.
4) By effectively monitoring operational data such as maintenance history, performance trends, meter readings, and operating conditions, organizations can proactively manage available resources such as inventory, equipment and skilled personnel to match them to asset maintenance demand.
5) Optimization of asset utilizations, scheduling and resources improves resource efficiency and enhances maintenance quality, maximizes resource availability including equipment and labor. Maintenance costs and work history are tracked at asset level.
6) Oracle eAM enables organizations to create and implement optimal and effective asset management strategies that can increase revenue and decrease costs. Both Preventive and Predictive Maintenance strategies are supported by eAM. It allows you to create alternate maintenance strategies for seasonal or production capacity changes. It supports sophisticated, condition-based maintenance strategies for property, plants and public infrastructure, improves operation performance, and with preventive and scheduled maintenance, increases safety, optimizes Scheduling and resource efficiency.
7) It eliminates the need for spreadsheets and disparate data repositories, by enabling companies to manage reactive, planned, preventive maintenance, and adopt a centralized, proactive strategy for managing asset maintenance across an enterprise.
8) Oracle eAM's single-instance design ensures best practices and quality compliance globally, eliminates excess and obsolete spare parts inventories, promotes environmental, health and safety policies, smoothes coordination of production and maintenance schedules and improves both the responsiveness and accuracy of contracted maintenance.
9) It bridges the gap between ERP/MRP solutions and Asset Maintenance for industries that rely heavily on Asset Maintenance Systems.
10) It is a lynchpin of the integrated workplace incorporating visual navigation for space planning and allocation, multi-channel service request processing, building systems maintenance and technology asset tracking.
11) eAM improves return on capital assets by integrating physical with financial aspects and supporting deep collaboration between project lifecycle and service lifecycle operations.
12) It integrates seamlessly with other modules of E-Business suite and is suitable for Metals/Mining, Manufacturing, Pulp/ Paper, Petrochemicals, Facilities and Education and many more assets.
--
Posted By OracleOnDemand to Oracle Applications at 12/28/2008 11:45:00 PM
1) An asset is an entity for which users can report problems. Assets can be cooling towers, cranes, buses, buildings, conveyors, or anything that needs work.
2) eAM creates and implements maintenance procedures for both assets and rebuildable Inventory items and takes care of comprehensive and routine maintenance requirements of asset intensive organizations. It effectively maintains assets such as vehicles, cranes and HVAC systems and rotable Inventory items such as motors and engines.
3) eAM enables users to optimally plan and schedule maintenance operations /activities with minimal disruptions to an organization's operations and productions. It measures performance and optimizes maintenance operations. It tracks the performance of the assets and rebuildable inventory items by using meters, quality plans and conditioning systems.
4) By effectively monitoring operational data such as maintenance history, performance trends, meter readings, and operating conditions, organizations can proactively manage available resources such as inventory, equipment and skilled personnel to match them to asset maintenance demand.
5) Optimization of asset utilizations, scheduling and resources improves resource efficiency and enhances maintenance quality, maximizes resource availability including equipment and labor. Maintenance costs and work history are tracked at asset level.
6) Oracle eAM enables organizations to create and implement optimal and effective asset management strategies that can increase revenue and decrease costs. Both Preventive and Predictive Maintenance strategies are supported by eAM. It allows you to create alternate maintenance strategies for seasonal or production capacity changes. It supports sophisticated, condition-based maintenance strategies for property, plants and public infrastructure, improves operation performance, and with preventive and scheduled maintenance, increases safety, optimizes Scheduling and resource efficiency.
7) It eliminates the need for spreadsheets and disparate data repositories, by enabling companies to manage reactive, planned, preventive maintenance, and adopt a centralized, proactive strategy for managing asset maintenance across an enterprise.
8) Oracle eAM's single-instance design ensures best practices and quality compliance globally, eliminates excess and obsolete spare parts inventories, promotes environmental, health and safety policies, smoothes coordination of production and maintenance schedules and improves both the responsiveness and accuracy of contracted maintenance.
9) It bridges the gap between ERP/MRP solutions and Asset Maintenance for industries that rely heavily on Asset Maintenance Systems.
10) It is a lynchpin of the integrated workplace incorporating visual navigation for space planning and allocation, multi-channel service request processing, building systems maintenance and technology asset tracking.
11) eAM improves return on capital assets by integrating physical with financial aspects and supporting deep collaboration between project lifecycle and service lifecycle operations.
12) It integrates seamlessly with other modules of E-Business suite and is suitable for Metals/Mining, Manufacturing, Pulp/ Paper, Petrochemicals, Facilities and Education and many more assets.
--
Posted By OracleOnDemand to Oracle Applications at 12/28/2008 11:45:00 PM
[Oracle Applications] Which are different types of discrete jobs ?
Which are different types of discrete jobs ?
There are 2 types of discrete jobs 1) Standard and 2) Non-Standard
Non Standard discrete jobs are further devided in to Non standard Asset jobs and non-standard expense jobs. Standard discrete jobs control the material, resources, and operations which are required to build an assembly and collect its manufacturing cost.
Some comparison is done as below:
1) Non-standard discrete jobs control material and collect costs for miscellaneous manufacturing activity. They may or may not build an assembly. This type of activity can include rework, field service repair, upgrade, disassembly, maintenance, engineering prototypes and other projects.
2) Non-standard jobs are more flexible than standard jobs. Because of this, they can be used to manage such different activities as rework, field service repair, upgrades, disassembly, maintenance, engineering prototypes and other miscellaneous projects.
3) MS/MRP module does not create planned orders or reschedule recommendations for non-standard jobs like standard jobs. You must manually define and reschedule non-standard jobs. However, if a non-standard job is assigned an assembly bill of material, a routing, or both, MS/MRP considers the job's material requirements as demand and its assemblies as supply. Oracle Capacity module considers resource load for non-standard jobs.
4) MS/MRP does not deduct scrapped assemblies from the MRP net quantity, or deduct the MRP net quantity by the item shrinkage rate for non-standard jobs. As such, you must identify planned assembly shrinkage by entering an MRP net quantity that is less than the job quantity.
5) Non-standard expense jobs are period costed and are not subject to cost updates, whereas standard discrete and asset type non-standard jobs are job costed i.e. costed when job is closed and are automatically revalued by the cost update.
6) Non-standard discrete jobs do not earn overhead on completion. Instead material overhead at completion is posted directly to the subinventory material overhead account.
7) Work in Process does not implement engineering change orders (ECOs) on non-standard jobs like it does on standard jobs
8) You can use a bill and routing from another assembly in non-standard jobs. For example, you can set up a standard upgrade routing to use for a group of assemblies.
9) For non-standard jobs, you can define bill of material loops, that is, you can define the assembly itself as a requirement on its bill. This is useful for upgrade, disassembly, and repair activities.
10) You can return a greater quantity of assemblies to non-standard discrete jobs than you completed into inventory.
11) Non standard asset jobs create assets/assemblies and are job costed. For example repair jobs where as Non-standard expense jobs do not create any assets and are period costed,For example maintenance jobs. Due to this, you need to define separate WIP accounting class for each.
--
Posted By OracleOnDemand to Oracle Applications at 12/28/2008 11:12:00 PM
There are 2 types of discrete jobs 1) Standard and 2) Non-Standard
Non Standard discrete jobs are further devided in to Non standard Asset jobs and non-standard expense jobs. Standard discrete jobs control the material, resources, and operations which are required to build an assembly and collect its manufacturing cost.
Some comparison is done as below:
1) Non-standard discrete jobs control material and collect costs for miscellaneous manufacturing activity. They may or may not build an assembly. This type of activity can include rework, field service repair, upgrade, disassembly, maintenance, engineering prototypes and other projects.
2) Non-standard jobs are more flexible than standard jobs. Because of this, they can be used to manage such different activities as rework, field service repair, upgrades, disassembly, maintenance, engineering prototypes and other miscellaneous projects.
3) MS/MRP module does not create planned orders or reschedule recommendations for non-standard jobs like standard jobs. You must manually define and reschedule non-standard jobs. However, if a non-standard job is assigned an assembly bill of material, a routing, or both, MS/MRP considers the job's material requirements as demand and its assemblies as supply. Oracle Capacity module considers resource load for non-standard jobs.
4) MS/MRP does not deduct scrapped assemblies from the MRP net quantity, or deduct the MRP net quantity by the item shrinkage rate for non-standard jobs. As such, you must identify planned assembly shrinkage by entering an MRP net quantity that is less than the job quantity.
5) Non-standard expense jobs are period costed and are not subject to cost updates, whereas standard discrete and asset type non-standard jobs are job costed i.e. costed when job is closed and are automatically revalued by the cost update.
6) Non-standard discrete jobs do not earn overhead on completion. Instead material overhead at completion is posted directly to the subinventory material overhead account.
7) Work in Process does not implement engineering change orders (ECOs) on non-standard jobs like it does on standard jobs
8) You can use a bill and routing from another assembly in non-standard jobs. For example, you can set up a standard upgrade routing to use for a group of assemblies.
9) For non-standard jobs, you can define bill of material loops, that is, you can define the assembly itself as a requirement on its bill. This is useful for upgrade, disassembly, and repair activities.
10) You can return a greater quantity of assemblies to non-standard discrete jobs than you completed into inventory.
11) Non standard asset jobs create assets/assemblies and are job costed. For example repair jobs where as Non-standard expense jobs do not create any assets and are period costed,For example maintenance jobs. Due to this, you need to define separate WIP accounting class for each.
--
Posted By OracleOnDemand to Oracle Applications at 12/28/2008 11:12:00 PM
[Oracle Applications] Which are the different methods for creating Discrete j...
Which are the different methods for creating Discrete jobs in Oracle WIP ?
You can create discrete jobs in the following ways:
a) Manually (both standard and non-standard discrete jobs)
b) Manually from a simulation of job (standard discrete jobs only)
c) Automatically using Oracle MRP module to plan your standard discrete production requirements
d) Automatically using Advanced Planning and Scheduling's High Level Scheduling Engine to schedule jobs and import them into Work in Process
e) Automatically (standard discrete jobs only) from final assembly orders for specific customer configurations and/or standard assemble-to-order(ATO)/configure-to-order items
f) Using the Work Order Interface to import planned orders and updated planned order recommendations
--
Posted By OracleOnDemand to Oracle Applications at 12/28/2008 11:03:00 PM
You can create discrete jobs in the following ways:
a) Manually (both standard and non-standard discrete jobs)
b) Manually from a simulation of job (standard discrete jobs only)
c) Automatically using Oracle MRP module to plan your standard discrete production requirements
d) Automatically using Advanced Planning and Scheduling's High Level Scheduling Engine to schedule jobs and import them into Work in Process
e) Automatically (standard discrete jobs only) from final assembly orders for specific customer configurations and/or standard assemble-to-order(ATO)/configure-to-order items
f) Using the Work Order Interface to import planned orders and updated planned order recommendations
--
Posted By OracleOnDemand to Oracle Applications at 12/28/2008 11:03:00 PM
[Oracle Applications] WIP:configuration Reservation Level
When I link a sales order to a job in the Discrete Job screen, after I complete this Discrete Job I have my Finish good item reserved in a "Subinventory 1", but I need to transfer it to "Subinventory 2", but I can't transfer because the material is reserved. I use 2 subinventories because one is for inspection and the second is the Sales Subinventory. What should I do?
You may set the Profile Option WIP:configuration Reservation Level to 'Item'. It indicates that the completed configuration (Assemblies) will be reserved at organization level in the inventory without subinventory and locator information. In that case, you will be able to transfer materials from Inspection Subinventory to Sales Subinventory.
--
Posted By OracleOnDemand to Oracle Applications at 12/28/2008 10:43:00 PM
You may set the Profile Option WIP:configuration Reservation Level to 'Item'. It indicates that the completed configuration (Assemblies) will be reserved at organization level in the inventory without subinventory and locator information. In that case, you will be able to transfer materials from Inspection Subinventory to Sales Subinventory.
--
Posted By OracleOnDemand to Oracle Applications at 12/28/2008 10:43:00 PM
[Oracle Applications] What is a Scheduled Group?
What is a Scheduled Group ?
A schedule group is group of flow schedules and discrete jobs which can be sequenced for the purpose of giving priority. Schedule groups are defined in the Define Schedule Groups window and can be optionally assigned to jobs, in the Discrete Jobs window, or to Flow schedules, in the Line Scheduling Workbench Options window. The schedule group assigned in the Line Scheduling Workbench Options window can be overridden in the Work Order-less Completions window, but only with a schedule group that is associated with a Flow schedule (an not associated with discrete job)
Sequencing is done by assigning a unique schedule number to each job or Flow schedule within a scheduled group.
You can assign flow schedules and discrete jobs to the schedule groups you define as per your requirement. Sequencing jobs and flow schedules within a schedule group makes it possible to prioritize, for example, by customer the jobs or Flow schedules being built on a specific production line.
You can update schedule groups but cannot delete schedule groups that are assigned to jobs and flow schedules. For example, you can create a Week01 schedule group to identify which jobs are to be released and built during the first week of your current production cycle.
--
Posted By OracleOnDemand to Oracle Applications at 12/28/2008 10:31:00 PM
A schedule group is group of flow schedules and discrete jobs which can be sequenced for the purpose of giving priority. Schedule groups are defined in the Define Schedule Groups window and can be optionally assigned to jobs, in the Discrete Jobs window, or to Flow schedules, in the Line Scheduling Workbench Options window. The schedule group assigned in the Line Scheduling Workbench Options window can be overridden in the Work Order-less Completions window, but only with a schedule group that is associated with a Flow schedule (an not associated with discrete job)
Sequencing is done by assigning a unique schedule number to each job or Flow schedule within a scheduled group.
You can assign flow schedules and discrete jobs to the schedule groups you define as per your requirement. Sequencing jobs and flow schedules within a schedule group makes it possible to prioritize, for example, by customer the jobs or Flow schedules being built on a specific production line.
You can update schedule groups but cannot delete schedule groups that are assigned to jobs and flow schedules. For example, you can create a Week01 schedule group to identify which jobs are to be released and built during the first week of your current production cycle.
--
Posted By OracleOnDemand to Oracle Applications at 12/28/2008 10:31:00 PM
[Oracle Applications] What are shop floor statuses in Oracle WIP ?
What are shop floor statuses in Oracle WIP ?
You define shop floor statuses in WIP and assign these statuses to intraoperation steps of the work in process routing operations. Shop floor statuses can be used to control/stopping shop floor move transactions due to various reasons. For example there could be some quality problem in the materials being used in manufacturing. You can view these statuses during move transactions you can define as many shop floor statuses as are required.
When assigned to an intraoperation step of an operation that is associated with a particular repetitive line and assembly, the status applies to all repetitive schedules building that assembly on that line. You can remove or unassign shop floor statuses once your problem is over.
--
Posted By OracleOnDemand to Oracle Applications at 12/28/2008 10:10:00 PM
You define shop floor statuses in WIP and assign these statuses to intraoperation steps of the work in process routing operations. Shop floor statuses can be used to control/stopping shop floor move transactions due to various reasons. For example there could be some quality problem in the materials being used in manufacturing. You can view these statuses during move transactions you can define as many shop floor statuses as are required.
When assigned to an intraoperation step of an operation that is associated with a particular repetitive line and assembly, the status applies to all repetitive schedules building that assembly on that line. You can remove or unassign shop floor statuses once your problem is over.
--
Posted By OracleOnDemand to Oracle Applications at 12/28/2008 10:10:00 PM
Saturday, December 27, 2008
[Oracle Applications] WIP accounting classes
What is WIP accounting class ?
Which are different accounting classes in WIP ?
Which different accounts are associated with it ?
An accounting class is a group of various General Ledger accounts which allows you to arrive at job cost, production cost and maintenance costs.
The following are different accounting classes in Oracle WIP:
1) Standard discrete
Standard discrete accounting classes can be used to group job costs for building subassemblies and finished goods on shop floor. You can define and attach this accounting classes so that you can separately value and report the costs associated with subassembly and finished goods production.
2) Asset non standard discrete
If you use non-standard discrete jobs to track production costs as assets, you can define and assign an accounting class with a type of asset non-standard. Asset non-standard discrete jobs are costed the same as standard discrete jobs. Valuation accounts are charged when material is issued to a job and final costs and variances are calculated and posted to the appropriate variance and valuation accounts when the job is closed.
3) Expense non-standard discrete
Non-standard discrete accounting classes can be used to group and report various types of non-standard production costs, such as field service repair. For example to track recurring expenses - machine maintenance or engineering projects- with non-standard jobs, you can define and assign an accounting class with a type ofexpense non-standard to these jobs. The valuation accounts carry the costs incurred on these expense jobs as an asset during the period and automatically writes them off to the variance accounts at period close.
4) Repetitive accounting class
Repetitive accounting classes are used to group production costs and must be assigned to each repetitive line/assembly association that is created. Every repetitive schedule for that assembly on that line uses these accounts.
5) Standard Lot based
Standard lot based jobs control the material, resources, and operations required to build an assembly and collect costs. When you build lot based jobs, the standard lot based accounting class is used to separately value and report costs associated with yielded production at each individual operation on the routing.
6) Expense non standard lot based
Expense non-standard lot based accoubting class jobs control material and collects costs for miscellaneous activity. These jobs are used for expense work orders for testing, prototypes, and rework where operation yield costing is not considered. You can perform all transactions (moves, jumps, scrap, splits, and update assemblies or routings) with the exception of job merge.
7) Maintenance accounting class
Maintenance accounting classes are used to group costs for work orders used in Oracle Enterprise Asset Management (eAM) Module . For example, if you are creating work orders for plant maintenance activities, you can define your accounting classes to separately value and report the costs related to asset.
--
Posted By OracleOnDemand to Oracle Applications at 12/28/2008 11:15:00 AM
Which are different accounting classes in WIP ?
Which different accounts are associated with it ?
An accounting class is a group of various General Ledger accounts which allows you to arrive at job cost, production cost and maintenance costs.
The following are different accounting classes in Oracle WIP:
1) Standard discrete
Standard discrete accounting classes can be used to group job costs for building subassemblies and finished goods on shop floor. You can define and attach this accounting classes so that you can separately value and report the costs associated with subassembly and finished goods production.
2) Asset non standard discrete
If you use non-standard discrete jobs to track production costs as assets, you can define and assign an accounting class with a type of asset non-standard. Asset non-standard discrete jobs are costed the same as standard discrete jobs. Valuation accounts are charged when material is issued to a job and final costs and variances are calculated and posted to the appropriate variance and valuation accounts when the job is closed.
3) Expense non-standard discrete
Non-standard discrete accounting classes can be used to group and report various types of non-standard production costs, such as field service repair. For example to track recurring expenses - machine maintenance or engineering projects- with non-standard jobs, you can define and assign an accounting class with a type ofexpense non-standard to these jobs. The valuation accounts carry the costs incurred on these expense jobs as an asset during the period and automatically writes them off to the variance accounts at period close.
4) Repetitive accounting class
Repetitive accounting classes are used to group production costs and must be assigned to each repetitive line/assembly association that is created. Every repetitive schedule for that assembly on that line uses these accounts.
5) Standard Lot based
Standard lot based jobs control the material, resources, and operations required to build an assembly and collect costs. When you build lot based jobs, the standard lot based accounting class is used to separately value and report costs associated with yielded production at each individual operation on the routing.
6) Expense non standard lot based
Expense non-standard lot based accoubting class jobs control material and collects costs for miscellaneous activity. These jobs are used for expense work orders for testing, prototypes, and rework where operation yield costing is not considered. You can perform all transactions (moves, jumps, scrap, splits, and update assemblies or routings) with the exception of job merge.
7) Maintenance accounting class
Maintenance accounting classes are used to group costs for work orders used in Oracle Enterprise Asset Management (eAM) Module . For example, if you are creating work orders for plant maintenance activities, you can define your accounting classes to separately value and report the costs related to asset.
--
Posted By OracleOnDemand to Oracle Applications at 12/28/2008 11:15:00 AM
Friday, December 26, 2008
[Oracle Applications] Explain the field 'Respond to sales order changes' in O...
Explain the field 'Respond to sales order changes' in Oracle WIP parameters ?
This field is applicable to configure-to-Order (CTO) sales orders and their related discrete jobs. It determines whether and how the system responds to changes to CTO sales orders and their linked and reserved discrete jobs/work orders (Both standard and Non-standard).
You can set the following options if a configured item is de-linked from a sales order or sales order line placed on hold.
a) Never
The corresponding work order will not be placed on hold if you de-link the configured item from the sales order, or if the sales order is placed on hold.
b) Always
The work order will be placed on hold if you de-link the configured item from the sales order, or if the sales order is placed on hold.
c) When Linked 1 to 1
The work order will be placed on hold if it is the only work order reserved to
that sales order. If there are more than one work orders for the sales order, this will not happen. If you cancel sales order lines with ATO items, this parameter, is ignored by the system.
You cannot cancel jobs linked to sales orders without first undoing the links between them.
--
Posted By OracleOnDemand to Oracle Applications at 12/27/2008 12:04:00 AM
This field is applicable to configure-to-Order (CTO) sales orders and their related discrete jobs. It determines whether and how the system responds to changes to CTO sales orders and their linked and reserved discrete jobs/work orders (Both standard and Non-standard).
You can set the following options if a configured item is de-linked from a sales order or sales order line placed on hold.
a) Never
The corresponding work order will not be placed on hold if you de-link the configured item from the sales order, or if the sales order is placed on hold.
b) Always
The work order will be placed on hold if you de-link the configured item from the sales order, or if the sales order is placed on hold.
c) When Linked 1 to 1
The work order will be placed on hold if it is the only work order reserved to
that sales order. If there are more than one work orders for the sales order, this will not happen. If you cancel sales order lines with ATO items, this parameter, is ignored by the system.
You cannot cancel jobs linked to sales orders without first undoing the links between them.
--
Posted By OracleOnDemand to Oracle Applications at 12/27/2008 12:04:00 AM
[Oracle Applications] What are intraoperation steps in Oracle WIP ?
What are intraoperation steps in Oracle WIP ?
There are 5 intra operation steps in WIP. The options are Queue, Run, To Move, Reject and Scrap. You can select intraoperation steps in WIP parameters by checking check boxes. It determines which intraoperation steps are enabled in WIP routing operations. The 'Queue' intraoperation step is automatically enabled for all operations and it cannot be disabled. The 'To Move' intraoperation step, even if disabled, is automatically enabled for the final operations in routings so that assemblies can be completed into inventory.
--
Posted By OracleOnDemand to Oracle Applications at 12/26/2008 11:50:00 PM
There are 5 intra operation steps in WIP. The options are Queue, Run, To Move, Reject and Scrap. You can select intraoperation steps in WIP parameters by checking check boxes. It determines which intraoperation steps are enabled in WIP routing operations. The 'Queue' intraoperation step is automatically enabled for all operations and it cannot be disabled. The 'To Move' intraoperation step, even if disabled, is automatically enabled for the final operations in routings so that assemblies can be completed into inventory.
--
Posted By OracleOnDemand to Oracle Applications at 12/26/2008 11:50:00 PM
[Oracle Applications] What is Assemble-to-Order(ATO) Manufacturing ?
What is Assemble-to-Order(ATO) Manufacturing ?
You can define available options in Bills of Material for unique product configurations. You can master schedule models and options and then create work orders to build these unique product configuration in WIP while maintaining control of inventory, planning and cost accounting. Bills of Material, WIP and Order Management/Shipping modules support building and shipping of ATO configurations. A discrete job is created from a configuration or an assemble to order item and then can be linked to a sales order.
--
Posted By OracleOnDemand to Oracle Applications at 12/26/2008 11:32:00 PM
You can define available options in Bills of Material for unique product configurations. You can master schedule models and options and then create work orders to build these unique product configuration in WIP while maintaining control of inventory, planning and cost accounting. Bills of Material, WIP and Order Management/Shipping modules support building and shipping of ATO configurations. A discrete job is created from a configuration or an assemble to order item and then can be linked to a sales order.
--
Posted By OracleOnDemand to Oracle Applications at 12/26/2008 11:32:00 PM
[Oracle Applications] What is Flow Manufacturing ?
What is Flow Manufacturing ?
Flow Manufacturing is an innovative manufacturing method which synchronizes production with customer demand.
The characteristics of flow processes are:
a) Straight and short product flow patterns
b) Make to order strategy
c) Single-piece production
d) Just-In-Time materials/pull/dependent demand scheduling
e) Short production cycle times
f) Highly flexible and responsive processes
g) Highly flexible machines and equipment
h) Quick changeover
i) Continuous flow work cells
j) Compressed space
k) Multi-skilled employees
l) Empowered employees
m) High first inspection - pass yields with major reductions in defects
Oracle Flow Manufacturing module supports the entire build-to-order manufacturing process which includes make-to-stock, configure-to-order, discrete-repetitive, assemble-to-order, and engineer-to-order manufacturing strategies and methods. It initiates schedules as soon as customer orders are received, and ensures shipment as soon as build is complete. Flow manufacturing employs pulls material using kanbans planning and backflushes material and costs upon completion. This in turn helps decrease inventories, optimize machine utilization, reduce response time to customer orders, and simplify shop floor activities.
Flow manufacturing production lines are designed to support the inter-mixed production of multiple products within a family on the same line at a constant rate. It can be used in Inventory module to replenish kanbans and in Work in Process to complete assemblies without having to create a job or a schedule (work order less job)
--
Posted By OracleOnDemand to Oracle Applications at 12/26/2008 11:10:00 PM
Flow Manufacturing is an innovative manufacturing method which synchronizes production with customer demand.
The characteristics of flow processes are:
a) Straight and short product flow patterns
b) Make to order strategy
c) Single-piece production
d) Just-In-Time materials/pull/dependent demand scheduling
e) Short production cycle times
f) Highly flexible and responsive processes
g) Highly flexible machines and equipment
h) Quick changeover
i) Continuous flow work cells
j) Compressed space
k) Multi-skilled employees
l) Empowered employees
m) High first inspection - pass yields with major reductions in defects
Oracle Flow Manufacturing module supports the entire build-to-order manufacturing process which includes make-to-stock, configure-to-order, discrete-repetitive, assemble-to-order, and engineer-to-order manufacturing strategies and methods. It initiates schedules as soon as customer orders are received, and ensures shipment as soon as build is complete. Flow manufacturing employs pulls material using kanbans planning and backflushes material and costs upon completion. This in turn helps decrease inventories, optimize machine utilization, reduce response time to customer orders, and simplify shop floor activities.
Flow manufacturing production lines are designed to support the inter-mixed production of multiple products within a family on the same line at a constant rate. It can be used in Inventory module to replenish kanbans and in Work in Process to complete assemblies without having to create a job or a schedule (work order less job)
--
Posted By OracleOnDemand to Oracle Applications at 12/26/2008 11:10:00 PM
[Oracle Applications] What is Project Manufacturing ?
What is Project Manufacturing ?
Large contracts or projects received by the companies can not be completely fulfilled by process manufacturing or disrete or repetitive manufacturing methods. It requires a separate manufacturing method known as project manufacturing. Project manufacturing meets demand driven production requirements for large contracts or projects. It allows you to plan, schedule, process and cost against a specific contract or a group of contracts or project for a specific customer.
Oracle Project Manufacturing supports companies in the Engineer-To-Order, Make-To-Order manufacturing strategies and Aerospace and Defense industries. These industries plan, track, procure, and cost based on project, contract, or Seiban numbers.
If Oracle Projects is installed and the Project References Enabled and Project Control Level parameters are set in the Organization Parameters window in Inventory module, you can assign project and, if required, task references to planned orders, jobs, purchase orders, sales orders, miscellaneous transaction and other entities within Oracle Manufacturing. If the Project Cost Collection Enabled parameter is also set in inventory organization parameters, you can optionally collect and transfer manufacturing cost to Oracle Projects module. Project costs are tracked by project/task and expenditure type.
--
Posted By OracleOnDemand to Oracle Applications at 12/26/2008 11:00:00 PM
Large contracts or projects received by the companies can not be completely fulfilled by process manufacturing or disrete or repetitive manufacturing methods. It requires a separate manufacturing method known as project manufacturing. Project manufacturing meets demand driven production requirements for large contracts or projects. It allows you to plan, schedule, process and cost against a specific contract or a group of contracts or project for a specific customer.
Oracle Project Manufacturing supports companies in the Engineer-To-Order, Make-To-Order manufacturing strategies and Aerospace and Defense industries. These industries plan, track, procure, and cost based on project, contract, or Seiban numbers.
If Oracle Projects is installed and the Project References Enabled and Project Control Level parameters are set in the Organization Parameters window in Inventory module, you can assign project and, if required, task references to planned orders, jobs, purchase orders, sales orders, miscellaneous transaction and other entities within Oracle Manufacturing. If the Project Cost Collection Enabled parameter is also set in inventory organization parameters, you can optionally collect and transfer manufacturing cost to Oracle Projects module. Project costs are tracked by project/task and expenditure type.
--
Posted By OracleOnDemand to Oracle Applications at 12/26/2008 11:00:00 PM
Thursday, December 25, 2008
[Oracle Applications] Oracle WIP - Move transaction parameters
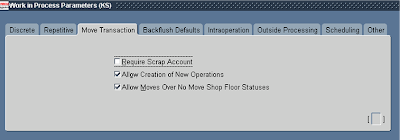
Explain move transaction parameters in Oracle WIP?
a) Require Scrap Account
This check box determines whether a scrap account is required when you use the Move Transactions window to move job and repetitive assemblies into and out of the Scrap intraoperation step of an operation. It also determines whether a scrap account is required when flow schedule assemblies are scrapped or returned from scrap through the Work Order-less Completions window. It is not madatory to keep scrap account. This parameter also determines how scrap transactions are processed. If you enter a scrap account, the system debits this account and credits the job or schedule elemental accounts through the operation at which the assemblies are scrapped. If you enter a reversing scrap transaction, the system credits this account and debits the job or schedule elemental accounts through the operation at which the assemblies are returned. If you do not provide a scrap account, the cost of scrap remains in the
job or schedule until job or period close and is then written off as a variance.
b) Allow Creation of New Operations
This check box determines whether you can or cannot add a new operation to a discrete job work in process routing during a move transaction. For example, you may want to add an operation to keep track of rework which you were not expecting.
c) Allow Moves Over No Move Shop Floor Statuses
This check box decides whether moves are disallowed if an intraoperation step that disallows moves exists at an autocharge operation and intraoperation step between the Setting Up From and To operations or at intervening intraoperation step at the From and To operations if they are direct charge. If an intraoperation step that disallows moves is found, a warning message is displayed and the move is disallowed. Allow Skipping Over No Move Statuses security function can be set to override no move shop floor statuses. Direct charge operations between the From and To Operations are not considered when the system checks for no move shop floor statuses. Scrap and Reject intraoperation steps at autocharge operations are also not considered.
For original post, please visit http://applearn.blogspot.com
--
Posted By OracleOnDemand to Oracle Applications at 12/26/2008 12:02:00 PM
Wednesday, December 24, 2008
[Oracle Applications] WIP Parameters - Backflush Transactions, Lot number gen...
Which parameters affect backflush Transactions?
a) Supply Subinventory
b) Supply Locator
c) Lot Selection Method
d) Alternate Lot Selection Method
e) Lot Verification
f) Release Backflush Components
g) Allow Quantity Changes During Backflush
How lot numbers are assigned to discrete jobs?
a) By Job Name: Lot numbers are based on the job name you enter when you define the job. This is the default.
b) Based on Inventory Rules: Lot numbers are based on the lot number rules which you defined in Inventory parameters in Inventory module
--
Posted By OracleOnDemand to Oracle Applications at 12/25/2008 12:06:00 AM
a) Supply Subinventory
b) Supply Locator
c) Lot Selection Method
d) Alternate Lot Selection Method
e) Lot Verification
f) Release Backflush Components
g) Allow Quantity Changes During Backflush
How lot numbers are assigned to discrete jobs?
a) By Job Name: Lot numbers are based on the job name you enter when you define the job. This is the default.
b) Based on Inventory Rules: Lot numbers are based on the lot number rules which you defined in Inventory parameters in Inventory module
--
Posted By OracleOnDemand to Oracle Applications at 12/25/2008 12:06:00 AM
[Oracle Applications] What is Backflush?
What is meant by backflush? When exactly backflush happens?
How can we detect that backflush is happening?
In Bills of Material module when you create a bill for any assembly or sub assembly or a finished good, you define component supply type for each component in a bill. These supply types are push, operation pull, assembly pull, Bulk, vendor/supplier, phantom etc. This Bills of material is used in Work in Process module for manufacturing a job. When you manufacture an assembly, it requires components at the shop floor as per the list given in a bill. If your supply type of a component is Push you have to manually issue components to shop floor for manufacturing process but if the supply type of a component is either assembly pull or operation pull, you need not to issue components manually to the shop floor but when a particular operation or an assembly is completed during manufacturing ie during move transactions or completion transactions, Oracle application system automatically backflushes components from the supply subinventory and locator Here ,backflushing means deduction( reducing) of required quantity from Inventory on hand quantity. In case of push supply type you have to deliver materials to shopfloor and deduct quantity yourself .Incase of backflushing you have to delivery materials to shopfloor and need not deduct quantity yourself but system( Oracle Applications) automatically deducts quantity from subinventory-locator on hand quantity when any assembly or an operation is completed in WIP module manufacturing process.
Once any assembly is completed in WIP, please go to inventory module and check the subinventory and locator quantity for the item for which assembly is completed. You will observe that on hand quantity has reduced .If total was 100 numbers and 10 numbers are pulled, by WIP assembly or operation pull, balance will be 90 numbers.
--
Posted By OracleOnDemand to Oracle Applications at 12/24/2008 11:10:00 PM
How can we detect that backflush is happening?
In Bills of Material module when you create a bill for any assembly or sub assembly or a finished good, you define component supply type for each component in a bill. These supply types are push, operation pull, assembly pull, Bulk, vendor/supplier, phantom etc. This Bills of material is used in Work in Process module for manufacturing a job. When you manufacture an assembly, it requires components at the shop floor as per the list given in a bill. If your supply type of a component is Push you have to manually issue components to shop floor for manufacturing process but if the supply type of a component is either assembly pull or operation pull, you need not to issue components manually to the shop floor but when a particular operation or an assembly is completed during manufacturing ie during move transactions or completion transactions, Oracle application system automatically backflushes components from the supply subinventory and locator Here ,backflushing means deduction( reducing) of required quantity from Inventory on hand quantity. In case of push supply type you have to deliver materials to shopfloor and deduct quantity yourself .Incase of backflushing you have to delivery materials to shopfloor and need not deduct quantity yourself but system( Oracle Applications) automatically deducts quantity from subinventory-locator on hand quantity when any assembly or an operation is completed in WIP module manufacturing process.
Once any assembly is completed in WIP, please go to inventory module and check the subinventory and locator quantity for the item for which assembly is completed. You will observe that on hand quantity has reduced .If total was 100 numbers and 10 numbers are pulled, by WIP assembly or operation pull, balance will be 90 numbers.
--
Posted By OracleOnDemand to Oracle Applications at 12/24/2008 11:10:00 PM
Monday, December 22, 2008
[Oracle Applications] Workflow Backgroud Process parameters
Workflow Backgroud Process parameters
What is Process Deferred =Yes, Process Timed Out= No ?
When the Workflow Engine initiates and performs a process in any Oracle applications module, it completes all necessary activities before continuing to the next eligible activity. In some cases, an activity being processed may require a large amount of processing resource or time to complete. Workflow module lets you manage the load on the Workflow Engine by setting up supplemental engines (known as background engine) to run these costly activities as background tasks. In these cases, the costly activity is deferred by the Workflow Engine and later it is run by a background engine. The main Workflow Engine can then continue to the next available activity, which may occur on some other parallel branch of the process.
A Background Engine is a supplemental Workflow Engine that processes deferred or timed out activities or stuck processes.(Proceses which are stuck because of workflow errors)
The above is possible only if you select the option "Process Deffered". Optinally, you can select the option "Process Timed out"=Yes if required.
--
Posted By OracleOnDemand to Oracle Applications at 12/23/2008 12:37:00 PM
What is Process Deferred =Yes, Process Timed Out= No ?
When the Workflow Engine initiates and performs a process in any Oracle applications module, it completes all necessary activities before continuing to the next eligible activity. In some cases, an activity being processed may require a large amount of processing resource or time to complete. Workflow module lets you manage the load on the Workflow Engine by setting up supplemental engines (known as background engine) to run these costly activities as background tasks. In these cases, the costly activity is deferred by the Workflow Engine and later it is run by a background engine. The main Workflow Engine can then continue to the next available activity, which may occur on some other parallel branch of the process.
A Background Engine is a supplemental Workflow Engine that processes deferred or timed out activities or stuck processes.(Proceses which are stuck because of workflow errors)
The above is possible only if you select the option "Process Deffered". Optinally, you can select the option "Process Timed out"=Yes if required.
--
Posted By OracleOnDemand to Oracle Applications at 12/23/2008 12:37:00 PM
Sunday, December 21, 2008
[Oracle Applications] Oracle WIP related Item attributes
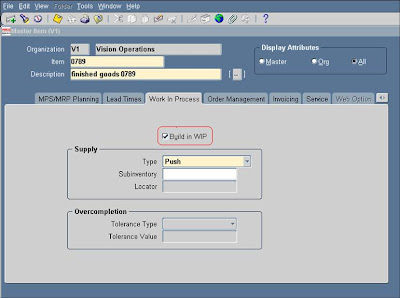
Describe WIP related Item attributes ?
a) Build in WIP
If you check this attribute, it indicates whether to create discrete jobs or repetitive assemblies in Work in Process module. This attribute must be turned off if the Inventory Item attribute is turned off or if the BOM item Type attribute is not set to Standard. You can not manufacture any item if item is not an inventory item and BOM item type is not standard. This attribute is optionally set by the Item Status code in inventory module
b) Supply Type
You can select a supply type attribute for components when you define an item in Item Master Organization. Supply types decides the method of supplying component materials to discrete jobs and repetitive job/schedules in WIP module. It also controls how materials are planned in MS/MRP module and how materials are costed in Cost Management module
c) Supply Subinventory
This attribute is controlled at the Organization level only. When you define an item in Item Master Organization, you can enter the primary subinventory from which to issue (push) or backflush (pull) an item to work in process during manufacturing.
d) Supply Locator
This attribute is controlled at the Organization level only. When you define an item in Item Master Organization, you can enter the supply locator from which to issue (push) or backflush (pull) an item to work in process. You can also define a WIP supply locator for any bill that uses this item; the bill supply locator overrides the supply locator which you define in Item Master Organization form. It is necesary to enter a WIP supply subinventory before you can enter a supply locator.
--
Posted By OracleOnDemand to Oracle Applications at 12/21/2008 10:36:00 PM
Saturday, December 20, 2008
[Oracle Applications] Oracle in Focus
Menswear brand Turtle has selected Oracle e-Business Suite R12 (Oracle Applications) to manage its operations in India
Oracle Financial Services Software (formerly known as i-flex solutions), a majority owned subsidiary of Oracle, on Wednesday announced Saudi Home Loans (SHL), the first fully specialized Islamic home finance company in the kingdom of Saudi Arabia, had gone live on Oracle Daybreak
Saline Water Conversion Corporation (SWCC),the Saudi utility giant will run Oracle ERP, Supply Chain and Asset Management applications in 30 plants spread across 17 locations
Al Othaim Holding, the largest grocery retailer in Saudi Arabia, selected Oracle as its strategic IT vendor Computer Sales
Redington India Ltd has announced that the Company has entered into a Distributor Agreement with M/s. Oracle India Pvt. Ltd for distribution of their range of products in India.
Wipro Infotech, the India and West Asian IT business division of Wipro, has opened a new application support centre in Hyderabad which will offer a new service – FAST-R (Flexible Application SupporT-Remotely) – to the company's customers in India
Cognizant has won a $50-100 million contract from one of its existing customers last month, which is among the top five American pharma companies
SEED Infotech, India's one of the leading technology training provider in association with Global Transformation Technologies (GTT) partnering with Qingdao Software Park, China had launched SEED IT Education China Limited
Wipro Technologies has teamed up with Oracle to launch a new "innovative solutions lab" at Wipro's Electronic City Facility in Bangalore
Regal Beloit Corporation, a manufacturer of electrical and mechanical motion control products, has deployed Oracle Business Intelligence Applications
Oracle Korea today announced that LG Electronics has successfully implemented the Oracle E-Business Suite Release 12 in 6 countries worldwide.
*Above is a collection of news highlights gathered from various sources for information purposes only. Please verify with concerned before using the above information in any kind of research, decision or documents.
--
Posted By OracleOnDemand to Oracle Applications at 12/20/2008 07:24:00 PM
Oracle Financial Services Software (formerly known as i-flex solutions), a majority owned subsidiary of Oracle, on Wednesday announced Saudi Home Loans (SHL), the first fully specialized Islamic home finance company in the kingdom of Saudi Arabia, had gone live on Oracle Daybreak
Saline Water Conversion Corporation (SWCC),the Saudi utility giant will run Oracle ERP, Supply Chain and Asset Management applications in 30 plants spread across 17 locations
Al Othaim Holding, the largest grocery retailer in Saudi Arabia, selected Oracle as its strategic IT vendor Computer Sales
Redington India Ltd has announced that the Company has entered into a Distributor Agreement with M/s. Oracle India Pvt. Ltd for distribution of their range of products in India.
Wipro Infotech, the India and West Asian IT business division of Wipro, has opened a new application support centre in Hyderabad which will offer a new service – FAST-R (Flexible Application SupporT-Remotely) – to the company's customers in India
Cognizant has won a $50-100 million contract from one of its existing customers last month, which is among the top five American pharma companies
SEED Infotech, India's one of the leading technology training provider in association with Global Transformation Technologies (GTT) partnering with Qingdao Software Park, China had launched SEED IT Education China Limited
Wipro Technologies has teamed up with Oracle to launch a new "innovative solutions lab" at Wipro's Electronic City Facility in Bangalore
Regal Beloit Corporation, a manufacturer of electrical and mechanical motion control products, has deployed Oracle Business Intelligence Applications
Oracle Korea today announced that LG Electronics has successfully implemented the Oracle E-Business Suite Release 12 in 6 countries worldwide.
*Above is a collection of news highlights gathered from various sources for information purposes only. Please verify with concerned before using the above information in any kind of research, decision or documents.
--
Posted By OracleOnDemand to Oracle Applications at 12/20/2008 07:24:00 PM
[Oracle Applications] 2M@applearn - Member of the Month - December 2008
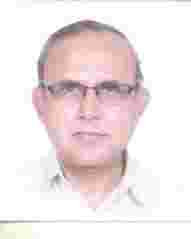
Member of the Month - December 2008
Pleased to announce that Vidyutkumar Desai is applearn 'member of the month' for December 2008. Vidyutkumar is a Bachelor of Textile Technology and DMS (Diploma in Management Studies).
With core expertise in Oracle Supply Chain and Manufacturing modules - Inventory, Purchasing, Order Management, Shipping, Bills of Material, Engineering, Work in Process, MS/MRP, Quality, EAM and Costing to name a few. Backed by 20 years industry experience, Vidyutkumar has @8 years experience in Oracle. His contribution to applearn community has been very helpful.
He likes listening to music, career guidence, touring, interecting with people and knowledge sharing. Sydney, Melbourne, New York, Hong Kong are some of his favourite places. Vidyutkumar has the below slogans as his favourites:
a) Vasudheiva kutumbakam which means 'The world is one (my) family'
b) A will will find a way
c) Time and tide wait for none
d) Make hay while the sun shines
e) I am with you till you do not want me in any way, any more.
Wish you all the best and looking forward for your continued contribution at applearn !!
--
Posted By OracleOnDemand to Oracle Applications at 12/20/2008 04:05:00 PM
[Oracle Applications] Supply Types in Oracle WIP
Explain the concept of Supply types in Oracle WIP? Describe each supply type in detail?
Supply types decides the method of supplying component materials to discrete jobs and repetitive schedules in WIP module. It also controls how materials are planned in MS/MRP module and how materials are costed in Cost Management module.
You can assign supply types to the items when you define in Inventory module. You can also assign supply types to components when you create bills of material in Bills of Material and Engineering modules. The following is a list of the WIP supply types and the way they work:
a)Push
Push components can be manually issued directly to discrete jobs and repetitive schedule as per requirements. You can specify the subinventory for items in Item definition form or in Bills or define default subinventory in WIP parameters form. Work in Process defaults the supply subinventory associated with the component.
b)Operation Pull:
Operation pull components that are assigned to backflush operations, are automatically backflushed (pulled) from inventory and issued to discrete jobs and repetitive schedules when assemblies are moved and completed at that operation i.e. when you complete backflush operations. Also, operation pull component that have not been backflushed because they are assigned to non-backflush operations prior to the backflush operation are also backflushed.
The Components are pulled from the supply subinventory assigned to the component. You cannot assign this supply type to an assenbly without a routing or a non-standard discrete job without a routing. You can assign this supply type to assemblies that have routings with no operations or when the routing has disabled operations. However, all components with a supply type of operation pull are automatically changed to assembly pull.
c)Assembly pull:
Assembly Pull components are issued (backflushed) to discrete jobs and repetitive schedules when you complete all operations on assemblies in Work in Process. They are pulled from the supply subinventory assigned to the component requirement.
If you want to assign pull components to a bill of material or job that is not associated with a routing, you must assign an Assembly Pull supply type, rather than operation pull supply type. You cannot assign this supply type to a non-standard discrete job if you have not specified an assembly or bill of material reference for that non standard discrete job.
d)Based on Bill:
When you define a discrete job or a repetitive line/assembly association in WIP, the supply type for the assembly defaults to Based on Bill and assembly components are supplied based upon their bill of material supply types. You can change the defaulted Based on Bill supply type that is assigned to jobs and schedules as you define them. The Based on Bill supply type is WIP specific.
If the supply type for a job or line/assembly association is changed, the new supply type is applied to all component material requirements. For example, if you change the supply type of a job assembly from Based on Bill to Assembly Pull, the supply types of all assembly components are changed to Assembly pull. You can update the supply types of individual material requirements using the Material Requirements window in WIP
The system automatically changes components with a supply type of Operation Pull to Assembly Pull, when the Based on Bill supply type is applied to a job or repetitive job/ schedule that has a bill of material but has no a routing or operations.
e)Bulk:
Bulk component requirements can be viewed and are displayed on reports and inquiry forms (that display components requirements) when you include Bulk components on a bill of material. They can be used to communicate to the shop floor that bulk components must be used but need not be transacted. You can choose specific components in the type field of WIP material transaction form for issuing bulk components.
Bulk components are not backflushed nor do they default when issuing all components for an assembly. You can, however, manually issue specific bulk components to a discrete job or repetitive schedule. This supply type is selected for components like screws,nuts,bolts,nails,etc where it is difficult and may not be necessary to transact the exact quantity used.
f)Supplier/Vendor:
Supplier component requirements can be included on bills of material. Requirements for supplier components are created when you define discrete jobs and repetitive schedules in Work in Process. Supplier component requirements can be viewed and are displayed on reports. They provide information on the component materials that your suppliers provide but need not be transacted. Supplier components are not backflushed nor do they default when issuing all components for an assembly. You can, however, manually issue specific supplier components to discrete jobs and repetitive schedules/job.
g)Phantoms:
Phantom components can be assigned to bill of material component subassemblies and subassembly items in BOM and Engineering. Components of phantom subassemblies are used as if they were tied directly to the parent assembly. Phantom supply types cannot be assigned to jobs and repetitive lines/assembly associations in Work in Process. When model or option class bills are components to another bill of material, that component supply type is phantom.
Phantoms behave normally when they are top level assemblies, such as when master scheduled or manufactured on a discrete job. As subassemblies, they lose their distinct identity and become a collection of their components. Phantom components (not the phantom itself) are included on discrete jobs and repetitive job/schedules and are listed on the Discrete Job and Repetitive Schedule Pick List Reports.
For original post, please visit http://applearn.blogspot.com
--
Posted By OracleOnDemand to Oracle Applications at 12/20/2008 02:31:00 PM
Supply types decides the method of supplying component materials to discrete jobs and repetitive schedules in WIP module. It also controls how materials are planned in MS/MRP module and how materials are costed in Cost Management module.
You can assign supply types to the items when you define in Inventory module. You can also assign supply types to components when you create bills of material in Bills of Material and Engineering modules. The following is a list of the WIP supply types and the way they work:
a)Push
Push components can be manually issued directly to discrete jobs and repetitive schedule as per requirements. You can specify the subinventory for items in Item definition form or in Bills or define default subinventory in WIP parameters form. Work in Process defaults the supply subinventory associated with the component.
b)Operation Pull:
Operation pull components that are assigned to backflush operations, are automatically backflushed (pulled) from inventory and issued to discrete jobs and repetitive schedules when assemblies are moved and completed at that operation i.e. when you complete backflush operations. Also, operation pull component that have not been backflushed because they are assigned to non-backflush operations prior to the backflush operation are also backflushed.
The Components are pulled from the supply subinventory assigned to the component. You cannot assign this supply type to an assenbly without a routing or a non-standard discrete job without a routing. You can assign this supply type to assemblies that have routings with no operations or when the routing has disabled operations. However, all components with a supply type of operation pull are automatically changed to assembly pull.
c)Assembly pull:
Assembly Pull components are issued (backflushed) to discrete jobs and repetitive schedules when you complete all operations on assemblies in Work in Process. They are pulled from the supply subinventory assigned to the component requirement.
If you want to assign pull components to a bill of material or job that is not associated with a routing, you must assign an Assembly Pull supply type, rather than operation pull supply type. You cannot assign this supply type to a non-standard discrete job if you have not specified an assembly or bill of material reference for that non standard discrete job.
d)Based on Bill:
When you define a discrete job or a repetitive line/assembly association in WIP, the supply type for the assembly defaults to Based on Bill and assembly components are supplied based upon their bill of material supply types. You can change the defaulted Based on Bill supply type that is assigned to jobs and schedules as you define them. The Based on Bill supply type is WIP specific.
If the supply type for a job or line/assembly association is changed, the new supply type is applied to all component material requirements. For example, if you change the supply type of a job assembly from Based on Bill to Assembly Pull, the supply types of all assembly components are changed to Assembly pull. You can update the supply types of individual material requirements using the Material Requirements window in WIP
The system automatically changes components with a supply type of Operation Pull to Assembly Pull, when the Based on Bill supply type is applied to a job or repetitive job/ schedule that has a bill of material but has no a routing or operations.
e)Bulk:
Bulk component requirements can be viewed and are displayed on reports and inquiry forms (that display components requirements) when you include Bulk components on a bill of material. They can be used to communicate to the shop floor that bulk components must be used but need not be transacted. You can choose specific components in the type field of WIP material transaction form for issuing bulk components.
Bulk components are not backflushed nor do they default when issuing all components for an assembly. You can, however, manually issue specific bulk components to a discrete job or repetitive schedule. This supply type is selected for components like screws,nuts,bolts,nails,etc where it is difficult and may not be necessary to transact the exact quantity used.
f)Supplier/Vendor:
Supplier component requirements can be included on bills of material. Requirements for supplier components are created when you define discrete jobs and repetitive schedules in Work in Process. Supplier component requirements can be viewed and are displayed on reports. They provide information on the component materials that your suppliers provide but need not be transacted. Supplier components are not backflushed nor do they default when issuing all components for an assembly. You can, however, manually issue specific supplier components to discrete jobs and repetitive schedules/job.
g)Phantoms:
Phantom components can be assigned to bill of material component subassemblies and subassembly items in BOM and Engineering. Components of phantom subassemblies are used as if they were tied directly to the parent assembly. Phantom supply types cannot be assigned to jobs and repetitive lines/assembly associations in Work in Process. When model or option class bills are components to another bill of material, that component supply type is phantom.
Phantoms behave normally when they are top level assemblies, such as when master scheduled or manufactured on a discrete job. As subassemblies, they lose their distinct identity and become a collection of their components. Phantom components (not the phantom itself) are included on discrete jobs and repetitive job/schedules and are listed on the Discrete Job and Repetitive Schedule Pick List Reports.
For original post, please visit http://applearn.blogspot.com
--
Posted By OracleOnDemand to Oracle Applications at 12/20/2008 02:31:00 PM
Thursday, December 18, 2008
[Oracle Applications] Oracle WIP setups & Open Interface
Why do you need to define WIP parameters?
You can use WIP parameters to define modes of operation and to assign default values for various work in process functions. You can only define one set of WIP parameters per inventory organization.
Which are optional implementation steps for WIP?
Define Production Lines
Define Repetitive Assemblies
Define Scheduled Groups
Define Employees
Define Employee Labor Rates
Define Shop floor Statuses
Define Job and Schedule documents
Define Operation Documents
Defining Report sets
What all can you import in WIP module?
a) Import move transactions from data collection devices, factory floor machines or controllers using the Open Move Transaction Interface
b) Import material transactions (component issue/return, assembly completion/return, replenishment) from data collection devices, custom data entry forms, and other manufacturing inventory systems using the Open Inventory Transaction Interface
c) Import resource transactions from data collection devices and labor tracking systems using the Open Resource Cost Transaction Interface
d) Import planned orders, update recommendations, and planned repetitive schedules directly from external sources using the Work Order Interface
e) Update scheduling dates at the operation or resource level using the Work Order Interface
--
Posted By OracleOnDemand to Oracle Applications at 12/18/2008 10:07:00 PM
You can use WIP parameters to define modes of operation and to assign default values for various work in process functions. You can only define one set of WIP parameters per inventory organization.
Which are optional implementation steps for WIP?
Define Production Lines
Define Repetitive Assemblies
Define Scheduled Groups
Define Employees
Define Employee Labor Rates
Define Shop floor Statuses
Define Job and Schedule documents
Define Operation Documents
Defining Report sets
What all can you import in WIP module?
a) Import move transactions from data collection devices, factory floor machines or controllers using the Open Move Transaction Interface
b) Import material transactions (component issue/return, assembly completion/return, replenishment) from data collection devices, custom data entry forms, and other manufacturing inventory systems using the Open Inventory Transaction Interface
c) Import resource transactions from data collection devices and labor tracking systems using the Open Resource Cost Transaction Interface
d) Import planned orders, update recommendations, and planned repetitive schedules directly from external sources using the Work Order Interface
e) Update scheduling dates at the operation or resource level using the Work Order Interface
--
Posted By OracleOnDemand to Oracle Applications at 12/18/2008 10:07:00 PM
Wednesday, December 17, 2008
[Oracle Applications] What is Process Manufacturing?
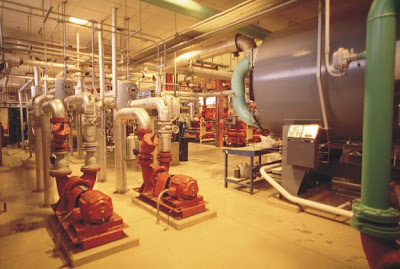
What is Process Manufacturing?
Process manufacturing is different from Discrete manufacturing.
Manufacturing is not in discrete batches but is a process of pressing/mixing/chemical processing/heating/boiling liquid/semi liquid/solid and powder or raw materials. Once you manufacture a product by using process manufacturing, the output can not be brought to it's original basic form.
For example orange juice with sugar added cannot be put back in to the Orange and Sugar seperately. On the other hand a computer manufactured by a discrete manufacturing process can be disassembled and the parts can be returned to stock to a large extent. Examples of process manufacturing are food products, beverages, paints & coatings, chemicals, specialty chemicals , pharmaceuticals, consumer packaged goods, Bulk drug pharmaceuticals, Nutraceutical, cosmeceutical and biotechnology industries. In Process Manufacturing, there are ingredients and not parts; there are formulas and not bill of materials; and bulk, not Unit of measure Each
For original post, please visit http://applearn.blogspot.com
--
Posted By OracleOnDemand to Oracle Applications at 12/18/2008 12:51:00 AM
Saturday, December 13, 2008
[Oracle Applications] Different manufacturing strategies
Which are different manufacturing strategies?
There are 4 manufacturing strategies
a) Make to stock(MTS)
b) Make to Order(MTO)
c) Assemble to Order(ATO)
d) Engineer to order(ETO)
In MTS, stock is created by companies for items without receiving an order from customer. Examples are manufacturing of refrigerators, washing nachines and Television sets. They are manufactured in a flow shop based on master schedule and stocked in finished goods subinventory until they are shipped to a cutomer.
MTO are manufactured after receiving customer order, which means customer is willing to accept longer delivery period. The examples are commercial dish washers and refrigerators for hotels. These items are produced in a flow shop or in job shop depending up on the range of product families produced by the factory. In order to reduce lead time the factory often uses ready components to manufacture a product.
In ATO, stock of existing items is kept on hand but they are sub assemblies, not the finished product. The company uses final assembly orders to put the finished product together according to specifications of the customer order. This involves some extra lead time but not as much as MTO. Private aircrafts, commercial trucks and computers are the examples of ATO. ATO items may be produced either in flow shop or job shop. ATO offers many variations in standard product because of the choices the customers have in deciding final product from options provided .
ETO item is built on the customer product specifications such as large commercial aircrafts. Such product can not be produces according to existing specifications of the company because some engineering skill is required to incorporate customer specifications in to the design of the final product. Companies using this manufacturing strategy, always quote longer lead time .The engineering and manufacturing costs involved are also high and are tracked for each order separately.
--
Posted By OracleOnDemand to Oracle Applications at 12/14/2008 11:59:00 AM
There are 4 manufacturing strategies
a) Make to stock(MTS)
b) Make to Order(MTO)
c) Assemble to Order(ATO)
d) Engineer to order(ETO)
In MTS, stock is created by companies for items without receiving an order from customer. Examples are manufacturing of refrigerators, washing nachines and Television sets. They are manufactured in a flow shop based on master schedule and stocked in finished goods subinventory until they are shipped to a cutomer.
MTO are manufactured after receiving customer order, which means customer is willing to accept longer delivery period. The examples are commercial dish washers and refrigerators for hotels. These items are produced in a flow shop or in job shop depending up on the range of product families produced by the factory. In order to reduce lead time the factory often uses ready components to manufacture a product.
In ATO, stock of existing items is kept on hand but they are sub assemblies, not the finished product. The company uses final assembly orders to put the finished product together according to specifications of the customer order. This involves some extra lead time but not as much as MTO. Private aircrafts, commercial trucks and computers are the examples of ATO. ATO items may be produced either in flow shop or job shop. ATO offers many variations in standard product because of the choices the customers have in deciding final product from options provided .
ETO item is built on the customer product specifications such as large commercial aircrafts. Such product can not be produces according to existing specifications of the company because some engineering skill is required to incorporate customer specifications in to the design of the final product. Companies using this manufacturing strategy, always quote longer lead time .The engineering and manufacturing costs involved are also high and are tracked for each order separately.
--
Posted By OracleOnDemand to Oracle Applications at 12/14/2008 11:59:00 AM
Friday, December 12, 2008
[Oracle Applications] What is Discrete Manufacturing?
What is Discrete Manufacturing?
1) Discrete manufacturing is a manufacturing process in which distinct items/products(which you can easily count, see and touch) are built or manufactured in discrete batches on manufacturing floor. It creates physical products which go directly to business and consumers, and assemblies that are used by other manufacturers. The resulting product is easily identifiable. It is different from process manufacturing where products are undifferentiated (can not tell the difference between one product and another) such as oil, natural gas and salt.
2) A typical characteristic of discrete manufacturing is the frequent switching from one manufactured product to another. The products are typically manufactured in individually defined lots, the sequence of work centers through production varying for each one of these. Costs are calculated on the basis of orders and individual lots.
3) Discrete manufacturing is also characterized by individual or separate unit production. Units can be produced in low volume with very high complexity or high volumes of low complexity. Low volume/high complexity production results in the need for an extremely flexible manufacturing system that can improve quality and time-to-market speed while cutting costs. High volume/low complexity production puts high premiums on inventory controls, lead times and reducing or limiting materials costs and waste
4) Discrete manufacturing typically involves the sequence of work centers through which the products can pass during production. This sequence can be varied as per requirement. The order of work centers is determined in routings, which can often be very complex. There can be waiting times between the individual work centers. Also, semi-finished products are frequently placed in interim storage prior to further processing
5) In discrete manufacturing, component materials are staged with specific reference to the individual production lots. Completion confirmations for the various steps and processes document the work progress and enable fine-tune controlling.
Examples are Transportation equipment, Automobiles, toys, Computer and accessories and electronic products, consumer electronics, furniture, Lego Blocks, Appliances and other house hold items, Industrial and electrical equipment, Medical equipment and supplies, Fabricated metal, furniture, recycling, pencil ,light bulb, telephone, bicycle, fuel pump, miscellaneous manufacturing as well as "big ticket" consumer and commercial goods like cars and airplanes, semi conductors, outfitting with industrial products, machine and plant engineering, right through to shipbuilding and aircraft construction. Fabricating products by assembling components and subsystems into larger systems. The automated assembly line is the prime example of discrete manufacturing such as in the making of automobiles, household appliances and computer systems. Discrete manufacturing systems typically deal with digital inputs to programmable logic controllers (PLCs) and programmable automation controllers (PACs) that cause motors and robotic devices to be activated. Fabricated Metal Products, Industrial and Commercial Machinery.
--
Posted By OracleOnDemand to Oracle Applications at 12/13/2008 10:44:00 AM
1) Discrete manufacturing is a manufacturing process in which distinct items/products(which you can easily count, see and touch) are built or manufactured in discrete batches on manufacturing floor. It creates physical products which go directly to business and consumers, and assemblies that are used by other manufacturers. The resulting product is easily identifiable. It is different from process manufacturing where products are undifferentiated (can not tell the difference between one product and another) such as oil, natural gas and salt.
2) A typical characteristic of discrete manufacturing is the frequent switching from one manufactured product to another. The products are typically manufactured in individually defined lots, the sequence of work centers through production varying for each one of these. Costs are calculated on the basis of orders and individual lots.
3) Discrete manufacturing is also characterized by individual or separate unit production. Units can be produced in low volume with very high complexity or high volumes of low complexity. Low volume/high complexity production results in the need for an extremely flexible manufacturing system that can improve quality and time-to-market speed while cutting costs. High volume/low complexity production puts high premiums on inventory controls, lead times and reducing or limiting materials costs and waste
4) Discrete manufacturing typically involves the sequence of work centers through which the products can pass during production. This sequence can be varied as per requirement. The order of work centers is determined in routings, which can often be very complex. There can be waiting times between the individual work centers. Also, semi-finished products are frequently placed in interim storage prior to further processing
5) In discrete manufacturing, component materials are staged with specific reference to the individual production lots. Completion confirmations for the various steps and processes document the work progress and enable fine-tune controlling.
Examples are Transportation equipment, Automobiles, toys, Computer and accessories and electronic products, consumer electronics, furniture, Lego Blocks, Appliances and other house hold items, Industrial and electrical equipment, Medical equipment and supplies, Fabricated metal, furniture, recycling, pencil ,light bulb, telephone, bicycle, fuel pump, miscellaneous manufacturing as well as "big ticket" consumer and commercial goods like cars and airplanes, semi conductors, outfitting with industrial products, machine and plant engineering, right through to shipbuilding and aircraft construction. Fabricating products by assembling components and subsystems into larger systems. The automated assembly line is the prime example of discrete manufacturing such as in the making of automobiles, household appliances and computer systems. Discrete manufacturing systems typically deal with digital inputs to programmable logic controllers (PLCs) and programmable automation controllers (PACs) that cause motors and robotic devices to be activated. Fabricated Metal Products, Industrial and Commercial Machinery.
--
Posted By OracleOnDemand to Oracle Applications at 12/13/2008 10:44:00 AM
Saturday, December 6, 2008
[Oracle Applications] Oracle Inventory - Interview questions & answers
1) Which are required steps in Inventory module set up?
Answer:
a) All the 6 key flexfields i.e Items, Item Catalog, Account Alias, Sales Order, Locator and Item Category
b) Organizations
c) Change Organizations
d) Intercompany Relations
e) Unit of Measure Classes
f)Subunventories
g)Item Attribute Controls, Categories
h)Default Category set
i)Item Statuses
j) Cost types
k)Profile Options
l)Inventory Accounting Periods
2) What do you mean by Required with Defaults Steps?
Answer:
Required Step With Defaults means that the setup functionality comes with pre-seeded, default values in the database; however, you should review those defaults /default values and decide whether to change them to suit your business needs
3)Which are Required with Defaults Steps in Inventory module?
Answer:
There are no such steps in Inventory module
4)There is no stock locator control in your Inventory organization.Do you still need to configure it?
Answer:
You need not to configure the flexfield in a specific way but you must still compile the Stock Locators key Flexfield because all Oracle Inventory transaction and on-hand inquiries and reports require a frozen flexfield definition
5) What is the use of a picking rule?
Answer:
When you pick release a sales order in Order Management module , Order Shipping Execution module ( which is a part of Order Management) submits requests to Oracle Inventory module which uses the information given in picking rule to give priority to pick units of an items and then it generates pick lists for sales orders
6) Can you apply material overheads to Average Costing Organization?
Answer:
No, you can not apply it to Average Costing Organization. However you can apply it to Standard Costing Organization
7) What is a Transaction Action?
Answer:
A transaction action is a predefined method of changing the quantity and/or location and/or cost of an item. It is used in Transaction Type form
8) How many Predefined Transaction Actions are available in Inventory module?
Answer:
You may use one of six predefined transaction actions: --issue from stores, subinventory transfer, direct organization transfer, intransit shipment, cost update and receipt into stores.
9)Can you do Inventory transactions in prior periods?
Answer:
Yes, you can do by setting the profile option INV: Transaction Date validation to Provide warning when date in past period or Allow date in any open period. It allows entry of a past date
10) Can you change customer item name or Item after you save it?
Answer:
Yes, you can change it if you have set the profile option INV: Updatable Customer Item to Yes and INV: Updatable item to Yes respectively
--
Posted By OracleOnDemand to Oracle Applications at 12/06/2008 11:17:00 PM
Answer:
a) All the 6 key flexfields i.e Items, Item Catalog, Account Alias, Sales Order, Locator and Item Category
b) Organizations
c) Change Organizations
d) Intercompany Relations
e) Unit of Measure Classes
f)Subunventories
g)Item Attribute Controls, Categories
h)Default Category set
i)Item Statuses
j) Cost types
k)Profile Options
l)Inventory Accounting Periods
2) What do you mean by Required with Defaults Steps?
Answer:
Required Step With Defaults means that the setup functionality comes with pre-seeded, default values in the database; however, you should review those defaults /default values and decide whether to change them to suit your business needs
3)Which are Required with Defaults Steps in Inventory module?
Answer:
There are no such steps in Inventory module
4)There is no stock locator control in your Inventory organization.Do you still need to configure it?
Answer:
You need not to configure the flexfield in a specific way but you must still compile the Stock Locators key Flexfield because all Oracle Inventory transaction and on-hand inquiries and reports require a frozen flexfield definition
5) What is the use of a picking rule?
Answer:
When you pick release a sales order in Order Management module , Order Shipping Execution module ( which is a part of Order Management) submits requests to Oracle Inventory module which uses the information given in picking rule to give priority to pick units of an items and then it generates pick lists for sales orders
6) Can you apply material overheads to Average Costing Organization?
Answer:
No, you can not apply it to Average Costing Organization. However you can apply it to Standard Costing Organization
7) What is a Transaction Action?
Answer:
A transaction action is a predefined method of changing the quantity and/or location and/or cost of an item. It is used in Transaction Type form
8) How many Predefined Transaction Actions are available in Inventory module?
Answer:
You may use one of six predefined transaction actions: --issue from stores, subinventory transfer, direct organization transfer, intransit shipment, cost update and receipt into stores.
9)Can you do Inventory transactions in prior periods?
Answer:
Yes, you can do by setting the profile option INV: Transaction Date validation to Provide warning when date in past period or Allow date in any open period. It allows entry of a past date
10) Can you change customer item name or Item after you save it?
Answer:
Yes, you can change it if you have set the profile option INV: Updatable Customer Item to Yes and INV: Updatable item to Yes respectively
--
Posted By OracleOnDemand to Oracle Applications at 12/06/2008 11:17:00 PM
Subscribe to:
Posts (Atom)